Flexible electronics, also known as flex circuits, is a technology for assembling electronic circuits by mounting electronic devices on flexible plastic substrates, such as polyimide, PEEK or transparent conductive polyester film. Additionally, flex circuits can be screen printed silver circuits on polyester. Flexible electronic assemblies may be manufactured using identical components used for rigid printed circuit boards, allowing the board to conform to a desired shape, or to flex during its use.

Flex circuits are often used as connectors in various applications where flexibility, space savings, or production constraints limit the serviceability of rigid circuit boards or hand wiring. A common application of flex circuits is in computer keyboards; most keyboards use flex circuits for the switch matrix.
Flexible circuits technology has a surprisingly long history. Patents issued at the turn of the 20th century show clear evidence that early researchers were envisioning ways of making flat conductors sandwiched between layers of insulating material to layout electrical circuits to serve in early telephony switching applications. One of the earliest descriptions of what could be called a flex circuit was unearthed by Dr Ken Gilleo and disclosed in an English patent by Albert Hansen in 1903 where Hansen described a construction consisting of flat metal conductors on paraffin coated paper. Thomas Edison’s lab books from the same period also indicate that he was thinking to coat patterns cellulose gum applied to linen paper with graphite powder to create what would have clearly been flexible circuits, though there is no evidence that it was reduced to practice.
In the 1947 publication "Printed Circuit Techniques" by Cledo Brunetti and Roger W. Curtis (National Bureau of Standards Circular 468 first issued 15 November 1947) the a brief discussion of creating circuits on what would have been flexible insulating materials (e.g. paper) indicated that the idea was in place and in the 1950s Sanders Associates' inventors (Nashua, NH) Victor Dahlgren and company founder Royden Sanders made significant strides developing and patenting processes for printing and etching flat conductors on flexible base materials to replace wire harnesses. An advertisement from the 1950 placed by Photocircuits Corporation in New York demonstrated their active interest in flexible circuits also. Today, flexible circuits which are also variously known around the world variously as flexible printed wiring, flex print, flexi circuits, are used many products. Large credit is due to the efforts of Japanese electronics packaging engineers who have found a countless new ways to employ flexible circuit technology. For the last decade, flexible circuits have remained one of the fastest growing of all interconnection product market segments.

ALCOM attracted over $50M in funding, creating the technology and intellectual property used in a range of flexible electronics devices developed by several spin-off companies as well as medium and large businesses in Northeast Ohio.
Flexible electronics have until recently been utilize for saving space, the use of bendable circuit boards for surface mounted components have evolved from Sculptured flex circuits to Double-sided flex circuits on from Multilayer flex circuits to Polymer thick film (PTF). Flex circuits are true printed circuits in that the conductors are actually printed onto a polymer base film. They are typically single conductor layer structures, however two or more metal layers can be printed sequentially with insulating layers printed between printed conductor layers. While lower in conductor conductivity and thus not suitable for all applications, PTF circuits have successfully served in a wide range of low power applications at slightly higher voltages. Keyboards are a common application, however, there are a wide range of potential applications for this cost effective approach to flex circuit manufacture.
Bioelectronics is a recently coined term for a field of research that works to establish a synergy between electronics and biology. One of the main forums for information about the field is the Elsevier journal Biosensors and Bioelectronics, published since 1990. The emerging field of Bioelectronics seeks to exploit biology in conjunction with electronics in a wider context encompassing, for example, biological fuel cells, bionics and biomaterials for information processing, information storage, electronic components and actuators. A key aspect is the interface between biological materials and micro- and nano-electronics. Much progress has been made in this field allowing artificial implants for cochlear implants, bionic eyes and pacemakers.
Modern methods of measuring the body's activty, such as electroencephalography (EEG), electrocardiography (ECG), and electromyography (EMG), use electrical signals to measure changes in brain, heart, and muscle activity, respectively. Unfortunately, they rely on bulky and uncomfortable electrodes that are mounted using adhesive tape and conductive gel or even needles. Because of this, these types of measurements are limited to research and hospital settings and typically used over short periods of time because the contacts can irritate skin.
A team, led by Zhenan Bao of Stanford University, has been working toward making stretchy, artificial skins from rubber and carbon nanotubes. The skins will feel like the real thing to the touch and they will have a sense of touch too, electronically detecting changes in strain and pressure from a stretch or a pinch.
In the short term, flexible, stretchable electronics could help make medical devices smarter, by integrating sensors into sutures, surgical gloves or balloon catheters that feel their way through the passageways of a heart. Incorporating electronics onto (and into) human bodies for everyday use may follow close behind.
Instead of trying to make traditional electronic materials flexible, Stanford’s Bao and colleagues are turning the goal around: They’re trying to make flexible materials electronic. By layering thin textured films with carbon nanotubes, Bao and her colleagues are figuring out how to make touch-sensitive artificial skin no rigid parts required. In many ways, Bao’s artificial skin behaves like the real thing. But it has one big hurdle to clear: It still uses wires to send its messages to a computer. If the skin ever made its way into a prosthetic, it would need to relay signals wirelessly to the wearer’s brain. “Ultimately we want the sensors to be talking directly to the neurons,” Bao says.
In 2010, John Rogers, Ph.D Fiorenzo Omenetto, Ph.D and colleagues tested a silk-coupled electronic device on a feline brain. They placed the silk-backed mesh circuit onto the visual cortex of an anesthetized cat and monitored brain activity. Compared to thicker devices, the mesh molded more closely to the brain and recorded stronger signals. In people, such flexible devices may one day control prosthetic arms, map brain activity or quell seizures in epileptic patients.
The simplest devices for recording from the brain are needle-like electrodes that can penetrate deep into brain tissue. More state-of-the-art devices, called micro-electrode arrays, consist of dozens of semi-flexible wire electrodes, usually fixed to rigid silicon grids that do not conform to the brain's shape. In people with epilepsy, the arrays could be used to detect when seizures first begin, and deliver pulses to shut the seizures down. In people with spinal cord injuries, the technology has promise for reading complex signals in the brain that direct movement, and routing those signals to healthy muscles or prosthetic devices.
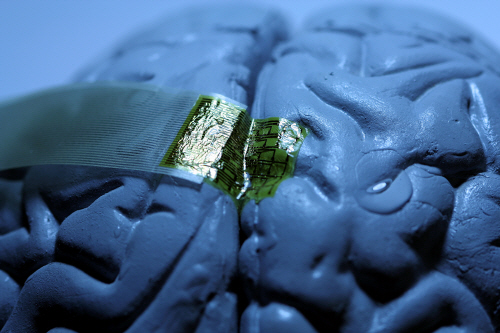
Evanston, Ill. Researchers from Northwestern University and the University of Illinois at Urbana-Champaign have developed “tattoo electronics” wireless electronics so flexible and thin they can be applied to the skin and forgotten. Yonggang Huang, who led the theory and design work at Northwestern, published in Science describes technology that allows electrical measurements (and other measurements, such as temperature and strain) using ultra-thin polymers with embedded circuit elements.

The device adheres to skin only using van der Waals forces the forces of attraction between atoms and molecules so no adhesive material is required. Between the flexibility and the lack of adhesive, you wouldn’t really notice one of these attached.
For a power supply, initial designs used silicon photovoltaic cells to generate electricity, but these are limited to microwatts due to the small area. Huang also explored wireless inductive power, where an external transmission coil matches the resonance frequency of a small inductive coil in the device (it's the same sort of tech that's used in wireless device chargers). This opens up the door for applications that need more power than solar can provide, or for devices that work in low-light conditions (under clothing, for example). The researchers also suggest future electrical storage using capacitors or batteries.
As demonstrations, the researchers used their devices to measure heartbeats on the chest (ECG), muscle contractions in the leg (EMG), and alpha waves through the forehead (EEG). The results were all high quality, comparing well against traditional electrode/conductive gel measurements in the same locations. In addition, the devices continuously captured data for six hours, and the devices could be worn for a full 24 hours without any degradation or skin irritation.
The Huang suggest there are a huge number of applications for this technology, including remote medical monitoring, biological/chemical sensing, human-machine interface, and covert communications. There are a couple areas where further development is needed, however: RF communication frequencies change when the circuits are stretched, and dead skin and sweat have to be dealt with during long-term use.
Flexible electronics may have started as a means to save space, but it is now continuing to prove useful in the field of bioelectronics for medical use. The introduction of flexible wiring and components not only will allow the integration of man and machine, in perhaps computer peripherals. But the idea of electronic tattoos for visually stunning and possibly non medical use of skin augmentation for vain purposes. Many people feel the use of electric tattoos will allow electronic tagging for criminal or eventual population control and monitoring. It's unsure if electronics will get this sophisticated, although electronic tattoos might evolve into the ultimate form or expression in the same way we personalize our phones...
No comments:
Post a Comment